Quality
Tool Room
One of Medicura’s key strengths is our state-of-the-art captive tool room, equipped with best-in-class CNC machines, including CNC Milling, CNC EDM, and CNC Wire Cut. Operated by a dedicated team of designers and engineers, Medicura Devices Pvt Ltd can design and manufacture most of our multi-cavity molds in-house. We also create Special Purpose Machines and fixtures necessary for the assembly of medical devices. This in-house capability allows us to rapidly develop, validate, and launch new models within a compressed timeframe. Furthermore, our in-house tooling equipment ensures a high degree of precision in components, achieving fine tolerance levels down to the micron.
Injection Moulding (Manufacturing of Components)
At Medicura Devices Private Limited, our Injection Moulding Section features state-of-the-art All-Electric Horizontal Moulding Machines, Vertical or Hub Moulding Machines, and Extrusion Lines within a Class 10,000/ISO Class 7 Clean Room. Most plastic components are moulded in-house using 100-ton and 180-ton Horizontal Moulding Machines. For specific insert-moulded components, we use Vertical Moulding equipment to combine metallic parts with plastic ones.
Additionally, we have in-house extrusion capabilities for producing rigid plastic tubes and soft Phthalate-Free PVC tubing. Our dedicated Quality Control team conducts in-process testing on all moulded and extruded parts during every shift to ensure consistent quality. Moulded components and tubing are stored in our Component Store, which also maintains clean room standards.
ASSEMBLY AREA (Automated Assembly Lines)
At Medicura Devices Private Limited Healthcare, we utilize Automated Assembly Lines for the production of devices such as IV Catheters and Three-Way Stop Cocks. These robotic assembly machines ensure a highly efficient and reliable assembly process. Equipped with in-line sensors, cameras, and testing equipment, our automated assembly lines guarantee a high degree of batch-to-batch consistency.
For other devices, we employ a semi-automated process using table-top fixtures operated by trained personnel. After assembly, all devices undergo visual inspection to ensure they conform to product requirements. This rigorous process ensures the highest quality standards for our manufactured medical devices.
Primary Packaging/Blister Packing
Fully-assembled devices are transferred to the Blister Packing section for packaging into rigid or soft unit packs. These unit packs are shaped according to the device design using forming and sealing dies on automated blister packaging equipment. Medicura Devices Private Limited uses only medical-grade paper for the top web and validated rigid or soft films for the bottom web, ensuring compliance with ISO 11607 international standards for packaging.
Additionally, we employ online printing technology to inscribe Batch Numbers, Expiry Dates, and Unique Device Identifiers (UDI) on all unit packs in real-time, ensuring traceability and quality control.
Final Inspection & Packing
After the product is secured inside a blister pack, it is transferred to the Cartoning Area or Final Inspection and Packing Section. In this area, dedicated personnel conduct a 100% inspection of each unit pack, checking for printing defects and other quality issues. Only after passing this rigorous inspection is the product packed into inner boxes and master cases, ensuring the highest quality standards are met before shipment.
Material Receipt Storage & Issue
The journey of every medical device at Medicura Devices Private Limited begins with the procurement of high-quality, pre-qualified, and standardized raw materials. We ensure that only validated raw materials are used in our medical devices. Upon receipt, all batches of raw materials undergo rigorous quality inspections, including physical and chemical testing. Until the Quality Control team releases these materials after completing the required tests, they are retained in the ‘Under Test’ section of our Raw Material Store.
Primary and secondary packaging materials, plastic granules, components, and chemicals are stored in separately demarcated areas of the store. A team of trained personnel ensures the traceability of raw materials used in all production lots, maintaining high standards of quality and accountability throughout the manufacturing process.
Ethylene Oxide Gas Sterilization
At Medicura Devices Private Limited, we employ terminal ethylene oxide (EO) sterilization for all sterile devices. In this process, the fully packed master cases are placed inside a stainless steel chamber, where they are exposed to ethylene oxide gas and steam under controlled conditions. The sterilization cycle for all devices is validated according to the ISO 11135 standard, ensuring compliance with international requirements.
Trained operators meticulously monitor and control the sterilization process parameters, including temperature, humidity, EO concentration, and exposure time. After sterilization, the finished products are moved to the quarantine area of the Finished Goods Store. Here, the products are stored until testing is completed and a release order is issued by the responsible personnel in the QC/QA departments.
Testing Facilities at Medicura Devices Private Limited
At Medicura Devices, we prioritize the highest standards of quality and safety. Our comprehensive testing facilities ensure that every product meets rigorous standards before reaching our customers. Our testing facilities include:
- Triple-Testing: We conduct thorough testing at three stages – Incoming, In-Process, and Finished Goods – to ensure quality at every step.
Comprehensive Testing: Our testing includes visual, dimensional, functional, and microbiological assessments to ensure compliance with product standards such as ISO 10555-1 for IV Catheters, ISO 80369-7 for Luers and Stop Cocks, and US Pharmacopoeia for Sterility.
In-House Physical/Functional Testing Laboratory: Equipped with advanced apparatus for Tensile Testing, Pressure Leakage Testing, Flow Rate Testing, Penetration Testing, and more.
Microbiological Testing Laboratory: Capable of performing Product Bio-Burden assessments, Clean Room Monitoring, and 14-day Sterility Testing.
With these state-of-the-art facilities, we ensure the highest quality and reliability of our medical devices.
Quality at Medicura Devices Private Limited Healthcare
At Medicura Devices Private Limited, we pride ourselves on our rigorous Quality Control measures, which include Triple-Testing at the Incoming, In-Process, and Finished Goods stages. Our team of dedicated and diligent QC and QA professionals conducts various visual, dimensional, functional, and microbiological tests to ensure compliance with product standards such as ISO 10555-1 and -5 for IV Catheters, ISO 80369-7 for Luers and Stop Cocks, and ISO 11070 for Hemodialysis Catheters and Vessel Dilators.
Our Key Quality Control Features:
- Comprehensive Testing: Our Physical Testing Laboratory operates 24-hours to ensure samples are drawn for functional tests such as flow rates, leakage, and penetration force from each production shift.
- Sterility and Microbiological Testing: Qualified microbiologists conduct Sterility Testing on all finished production lots as per US Pharmacopoeia, in addition to other microbiological evaluations for product and environmental bio-burden.
- Validated Processes: All production processes and equipment are validated periodically to ensure highly reliable and repeatable manufacturing.
- Regulatory Compliance: Our dedicated in-house QA and Regulatory team ensures that we meet and exceed stringent international standards. This enables us to register our products in multiple countries worldwide and satisfy documentary requirements of customers and regulators.
Certifications and Approvals:
- ISO 13485:2016 Certification
- MDSAP Certification
- CE Certification
- USFDA
Core Values:
- Empathy: Every Medicura Devices employee is committed to understanding and prioritizing the well-being of end-users.
- Discipline: We maintain an uncompromising adherence to strict tolerances at every stage of quality control.
- Standardization: Our automated and tightly controlled environment ensures consistency and standardization in all our products.
Quality Objectives
- Customer-Centric Product Quality: To produce quality products with built-in safety that meet well-defined customer needs, uses, and purposes.
- Regulatory Compliance: To comply with all statutory and regulatory requirements.
- Resource Efficiency: To utilize resources judiciously and efficiently, focusing on the conservation of water and energy.
- Innovation and Development: To promote innovations and the development of new products and processes.
- Process Capability Monitoring: To monitor and enhance process capability by adopting Statistical Quality Control, Total Quality Management, Total Productive Maintenance, and similar Quality Management tools.
- CE Guidelines Adherence: To adhere to CE guidelines and provisions.
- Customer Satisfaction Improvement: To achieve continual improvement in customer satisfaction concerning product quality, availability, and services.
- Employee Competence: To improve the competence and skills of each employee by identifying current and future requirements and bridging gaps through training and multi-skilling.
- Rejection Control: To control and contain the levels of rejection and scrap.
- Motivated Workforce: To develop a team of motivated, dedicated, and devoted workforce that encourages professional excellence.
To continue to transform and increase access to care for patients around the world, we are investing in new collaborations, partnering with world-renowned institutions, seeking out the next generation of innovators in healthcare, and funding the pursuit of new discoveries and research. This dedication ensures that we are fostering the next generation of innovation in medical care and technology.
In-House development
We understand that the first step to living your best life is good health. Everything we make is designed to help you achieve that. This commitment drives us to develop life-changing technologies that keep your body healthy and nourished at every stage of life, help you feel and move better, and bring you the information, medicines, and breakthroughs you need to manage your health. Our purpose is to make the world a better place by delivering these transformative health technologies to those who need them most. That’s our commitment to helping you live your best life.
Mission
“At Medicura Devices Private Limited, our mission is to advance global healthcare by delivering innovative and high-quality medical devices. We are committed to improving patient care by providing safe and reliable products to healthcare professionals and institutions worldwide. Our focus on research, development, and compliance with international standards drives us to be a trusted partner in the medical device industry.”
Vision
“Our vision at Medicura Devices Private Limited is to be a leading force in the global medical device manufacturing sector. We aspire to continuously innovate, enhance our product offerings, and expand our global reach. We aim to set new industry benchmarks for quality and reliability, ensuring that healthcare providers and patients receive the best possible solutions. Our dedication to sustainability, compliance, and excellence guides us towards a future where healthcare is advanced, accessible, and safer for all.”
Tool Room
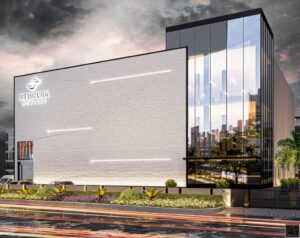
A key strength at Medicura is our state-of-the art captive tool room with best-in-class CNC Machines including CNC Milling, CNC EDM and CNC Wire Cut. Operated up by a dedicated team of designers and engineers, Medicura devices pvt ltd is able to design and manufacture most of our multi-cavity moulds in-house, in addition to Special Purpose Machines and fixtures required for assembly of medical devices. This in-house capability ensures that we are able to rapidly develop, validate and launch new models in a compressed time-frame. Additionally, having our in-house tooling equipment enables us to ensure a high degree of precision in the components with fine tolerance levels on the micron level.
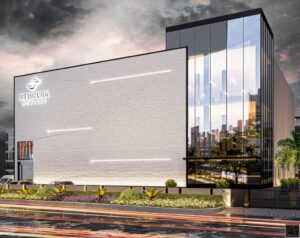
Injection Moulding (Manufacturing of Components)
Our Injection Moulding Section houses All-Electric Horizontal Moulding Machines, Vertical or Hub Moulding Machines and Extrusion Lines in a Class 10,000/ISO Class 7 Clean Room. The majority of plastic components are moulded in-house at Medicura Devices private limited on 100-ton and 180-ton Horizontal Moulding Machines. Additionally, for certain insert-moulded components, Vertical Moulding equipment are used to mate metallic parts with plastic ones. Medicura Devices private limited also has in-house extrusion capabilities for rigid plastic tubes as well as soft Phthalate-Free PVC tubing. Our team of dedicated Quality Control professionals conducts in-process testing on all moulded and extruded parts for every shift. Moulded Components and tubing are stored prior to issue in our Component Store, also a Class Room.Device Assembly
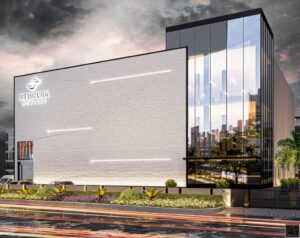
Primary Packaging/Blister Packing
Fully-assembled devices are moved into the Blister Packing section for packaging into rigid or soft unit packs. These Unit Packs are given specific shapes based on the device design with forming and sealing dies loaded onto automated blister packaging equipment. Medicura Devices private limited uses only Medical-Grade Paper as the Top-Web and Validated Rigid or Soft Films for the Bottom Web to ensure compliance with ISO 11607 international standard for packaging. Importantly, Medicura Devices private limited employs online printing technology for real-time inscription of Batch Numbers, Expiry Dates and Unique Device Identifiers (UDI) on all unit packs.
Final Inspection & Packing (Cartoning Area)
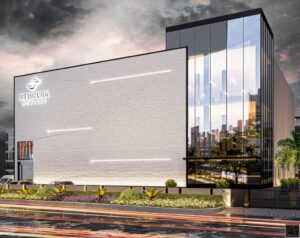
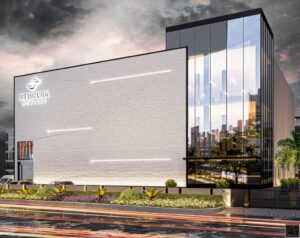
Material Receipt Storage & Issue
The journey of every medical device begins with the procurement of high-quality, pre-qualified and standardized raw materials. At Medicura Devices private limited, we ensure that only validated raw materials are used in our medical devices. Upon receipt, all batches of raw materials are subjected to rigorous quality inspections at the incoming stage, including physical and chemical testing. Until such time that the QC releases these materials after completion of required tests, they are retained in the ‘Under Test’ section of our Raw Material Store. Primary and Secondary Packaging Material, Plastic Granules, Components and Chemicals are stored in separately demarcated areas of the Store. Traceability of raw materials used in all production lots is ensured by a team of trained personnel tasked with issuing these to shop floors.Ethylene Oxide Gas Sterilization
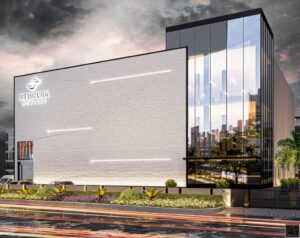
At Medicura Devices private limited, we employ Terminal Ethylene Oxide Sterilization for all sterile devices. This process requires the finally packed master cases to be placed inside a Stainless Steel Chamber where it is exposed to ethylene oxide gas and steam under controlled conditions. The Sterilization Cycle for all devices is validated as per the ISO-11135 Standard to conform with international requirements. Trained Operators monitor and ensure strict control of parameters of the sterilization process, namely Temperature, Humidity, EO Concentration and Time of Exposure. After sterilization, the finished product is moved into the Quarantine area of the Finished Goods Store. Here product is stored until testing is completed and Release Order is issued by responsible persons in the QC/QA functions.
Testing Facilities at Medicura Devices private limited
- Triple-Testing, i.e. testing at the Incoming, In-Process and Finished Goods Stages.
- Visual, dimensional, functional and microbiological tests to ensure compliance with product standards such as ISO 10555-1 for IV Catheters, ISO 80369-7 for Luers and Stop Cocks and US Pharmacopoeia for Sterility.
- In-House fully equipped Physical/Functional Testing Laboratory with apparatus for Tensile Testing, Pressure Leakage Testing, Flow Rate Testing, Penetration Testing, etc.
- Micro-biological Testing Laboratory for Product Bio-Burden, Clean Room Monitoring as well as 14-day Sterility Testing.
Quality at Medicura Devices private limited Healthcare
Medicura Devices private limited prides itself on rigorous Quality Control with Triple-Testing, i.e. testing at the Incoming, In-Process and Finished Goods Stages. Our team of dedicated and diligent QC and QA professionals conduct various visual, dimensional, functional and microbiological tests to ensure compliance with product standards such as ISO 10555-1 and -5 for IV Catheters, ISO 80369-7 for Luers and Stop Cocks and ISO 11070 for Hemodialysis Catheters and Vessel Dilators. The Physical Testing Laboratory operates 24-hours to ensure samples are drawn for functional tests such as flow rates, leakage and penetration force from each production shift. Qualified micro-biologists conduct Sterility Testing on all finished production lots as per US Pharmacopoeia, in addition to other micro-biological evaluation for product and environment bio-burden. Furthermore, all production processes and equipment are Validated on a periodic basis to ensure highly reliable and repeatable manufacturing. Our dedicated and in-house QA and Regulatory team ensures that we continue to meet and exceed the stringent requirements of international standards. This enables us to register our products in multiple countries worldwide and satisfy documentary requirements of customers as well as regulators. Today, Medicura Devices private limited holds ISO 13485:2016 as well as MDSAP Certification from TUV Sud, along with CE Certification from DNV Product Assurance, Norway, in addition to USFDA Registration and 510(k) Approvals.
Medicura Devices private limited strives to provide the highest-quality medical devices by inculcating:
- Empathy with end users and a deep concern for their well being in every single Medicura Devices private limited employee.
- Discipline and an uncompromising adherence to strict tolerances at every stage of quality control.
- Standardization in all products through an automated and tightly controlled environment.
Quality Objectives
- To produce quality products with built-in safety to meet well defined need, use and purpose of customers.
- To comply with statutory and regulatory requirements.
- Judicious and efficient utilization of resources. Conservatiom of water and energy.
- Promoting innovations and development of new products/processes.
- Monitoring and enhancing process capability by adopting Statistical Quality Control, Total Quality Management and total Productive Maintenance and similar Quality Management Tools.
- Adherence to CE guidelines and provisions.
- To achieve Continual Improvement in Customer Satisfaction in terms of Product Quality, Availability and Services.
- To improve competence and skill of each employee by identifying the current and future requirements and bridging the gap by providing training and multi-skilling.
- To control and contain the level of rejection/scrap.
- To develop a team of motivated, dedicated and devoted workforce that encourages professional excellence.
To continue to transform and increase access to care for patients around the world, we are investing in new collaborations, partnering with world-renowned institutions, seeking out the next-generation of innovators in healthcare and funding the pursuit of new discoveries and research. Fostering the Next Generation of Innovation
In-House development
We understand that the first step to living your best life is good health. Everything we make is designed to help you do just that. That’s our commitment to building life-changing technologies that keep your body healthy and nourished at every stage of life, help you feel and move better, and bring you information, medicines and breakthroughs to manage your health. Our purpose is to make the world a better place by bringing life-changing health technologies to the people who need them. That’s our commitment to helping you live your best life.
Mission
“At Medicura Devices Private Limited, our mission is to advance global healthcare by delivering innovative and high-quality medical devices. We are committed to improving patient care by providing safe and reliable products to healthcare professionals and institutions worldwide. Our focus on research, development, and compliance with international standards drives us to be a trusted partner in the medical device industry.”
Vision
“Our vision at Medicura Devices Private Limited is to be a leading force in the global medical device manufacturing sector. We aspire to continuously innovate, enhance our product offerings, and expand our global reach. We aim to set new industry benchmarks for quality and reliability, ensuring that healthcare providers and patients receive the best possible solutions. Our dedication to sustainability, compliance, and excellence guides us towards a future where healthcare is advanced, accessible, and safer for all.”
Call us for an appointment
+91 9877893322
Feel free to contact us.
info@medicuradevices.com
View Map